Home::News & MediaPress ReleasesLianhe News Network - Intelligent Automation Magazine - Use CNC value-added to seize the International Cup
Lianhe News Network - Intelligent Automation Magazine - Use CNC value-added to seize the International Cup
2020/05/11
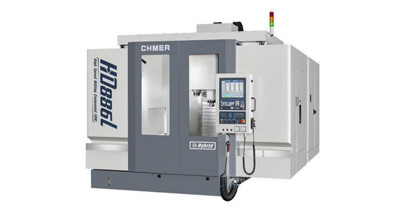
In the past, domestic CNC numerical control systems were less favored by the export-oriented machine tool industry, but as they moved towards intelligent and digital transformation and upgrading, they also began to deeply integrate and form alliances with domestic and foreign major manufacturers, and successively won the Taiwan Excellence Award Or repeated good news at major domestic and foreign exhibitions such as TIMTOS and JIMTOF.
Especially since the Sino-US trade war and the COVID-19 epidemic have followed, the global production chain has been full of turbulence and uncertainty. It is expected that due to the displacement of production sectors in the future, terminal manufacturing customers of machine tools will have to Only by accelerating the awareness of smart manufacturing can we be able to flexibly reduce/increase production in the short term; and allocate the demand for shortage/resumption of production manpower and remote work information security during the epidemic prevention period. It will be helpful to speed up intelligence sharing, pass certification, and even prepare in advance for urgent orders in the second half of the year when countries are reorganizing their supply chains after the epidemic is over.
Shunpeng supports CHMER research and development, progressing from single-machine compounding to intelligence.
In Taiwan, there is also CHMER, a major machine tool manufacturer that has been committed to "non-traditional machining" solutions in recent years. It targets small and medium-sized enterprise job shop customers who have grown significantly in domestic and foreign markets in the past 10 years and only require rapid production. In addition to fully supporting the CNC numerical control system required by the parent company, its subsidiary Shunpeng Technology has also begun to contact other external machine tool manufacturers for sporadic orders.
However, the biggest problem encountered in promoting complete line/factory automation in the mold industry may be that a small number of diverse molding processors have higher profits than traditional cutting processors, and they pay more attention to the quality and stability of products rather than the entire line. , the machine utilization rate of multi-station processing often makes it impossible to plan a standard process, and "cannot produce specifications, and it is even more difficult to accept." Therefore, Shunpeng Technology is still positioned to assist single-machine compounding and intelligence in the era of Industry 4.0. .
It also supports CHMER's launch of the world's first commercialized high-speed milling electric discharge composite machining machine in 2019 TIMTOS, which uses five-axis synchronous CNC controller hardware and software independently developed by Shunpeng Technology and high-thrust linear motors, and is equipped with a permanent magnet synchronous spindle (PMSM). ), high-resolution optical rulers are fully closed-loop servo controlled. Because the dual spindles adopt air pressure balance devices, they can achieve high reactivity and precise positioning, greatly improving processing accuracy and service life; they can even be equipped with A/C cradle-type four- and five-axis axes. , and can also be used to process complex or curved workpieces required for aerospace, LED molds, and medical materials.
It includes the CIAS HMC software specially developed for the CHMER smart high-speed processing machine App system. The comprehensive IoT modules that can be provided through the cloud are divided into: management module, intelligent processing module, energy saving and temperature management module, consumables and maintenance Modules, etc., using the modular electronic control system independently developed by Shunpeng Technology, can automatically alert when the machine is abnormal or malfunctioning, and notify quick maintenance.
And because all information is monitored by mobile phones, instantaneous power consumption and processing speed can be monitored remotely at any time, making it easier for customers to understand the processing status of the machine and more effectively manage work and energy consumption; and through the intelligent self-diagnosis function analyzed by the controller , real-time analysis of the usage status of each machine, or sending machine usage information via mobile phone to improve work efficiency and convenience.
If the initial mass production will be introduced into aerospace, automotive and other large-scale mold processing applications that require multi-station processing, we will help customers integrate multi-stage processes to process molds without wasting time on loading/unloading or recalibration, which may cause position errors or increase cycle time. And have to choose between accuracy, efficiency and other advantages.
With this One Shop (one-stop) processing, you can first complete rough/finish milling, or process hard, brittle, and difficult-to-cut materials, and then process large-scale depth/width ratio molds for the aerospace and automotive industries through electrical discharge. Reduce the time and cost of replacing tools due to wear; you can also use the automatic front door opening device and equipped with robots to achieve intelligent automated processing and manufacturing. It has won the TIMTOS R&D Innovation Competition Excellence Award that year and the 2020 Taiwan Excellence Award Silver Award.